For Good: We Meet the Creative Couple Behind Great Wrap
Our ‘For Good’ series are a set of conversations with talented people behind some of our favorite environmentally conscious brands. As our team at IN BED continue to work towards our own goals around environmental and social impact we are continuously inspired by others re-thinking what it means to create through a more sustainable lens.
In this feature we chat to Julia and Jordy Kay, the founders of compostable cling wrap brand Great Wrap, who take potato waste and turn it into a wrap that breaks down in home compost in under 180 days(!). We spoke to the couple about the path to building their business, the science behind their industry changing product, and their vision for the future of Great Wrap.
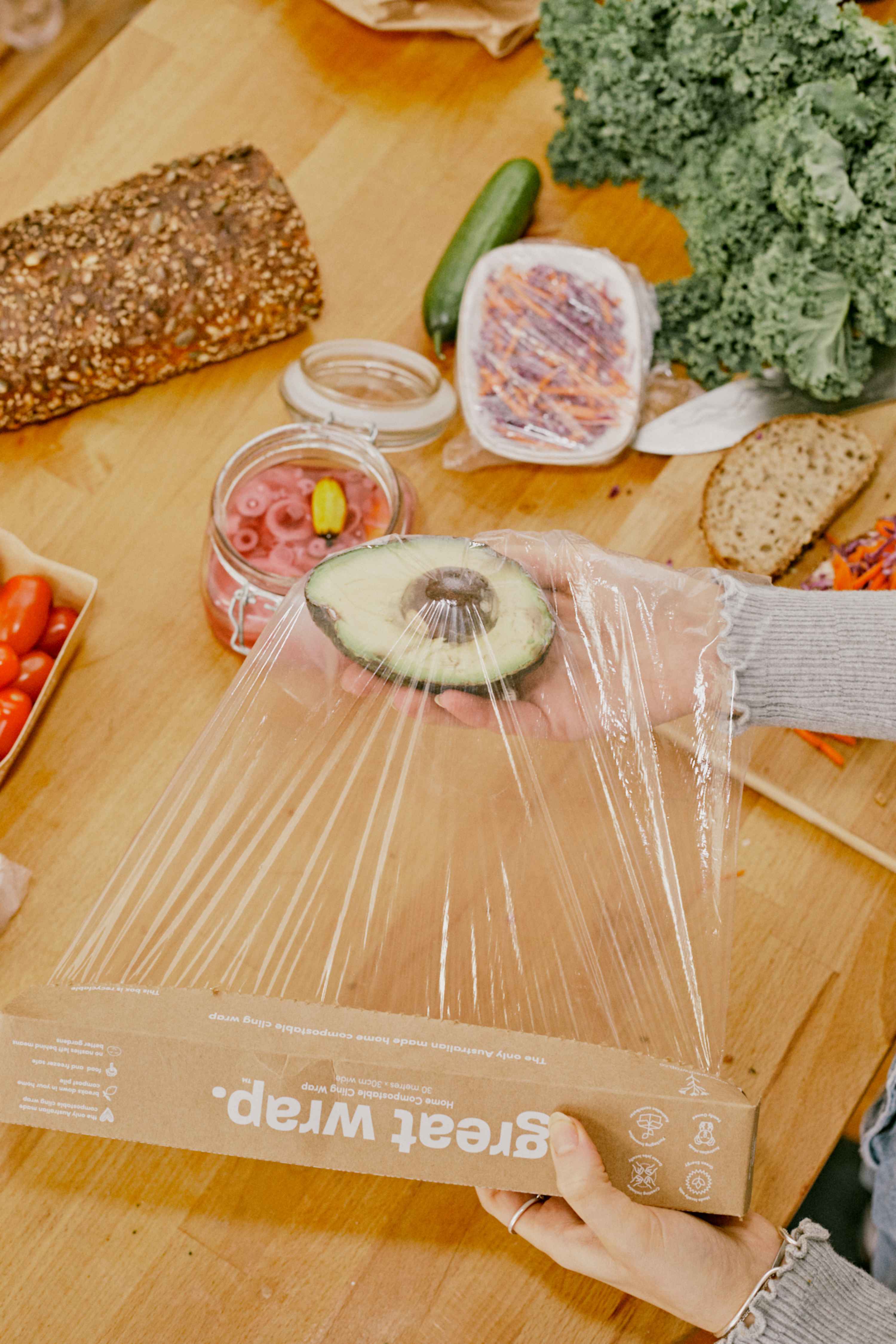
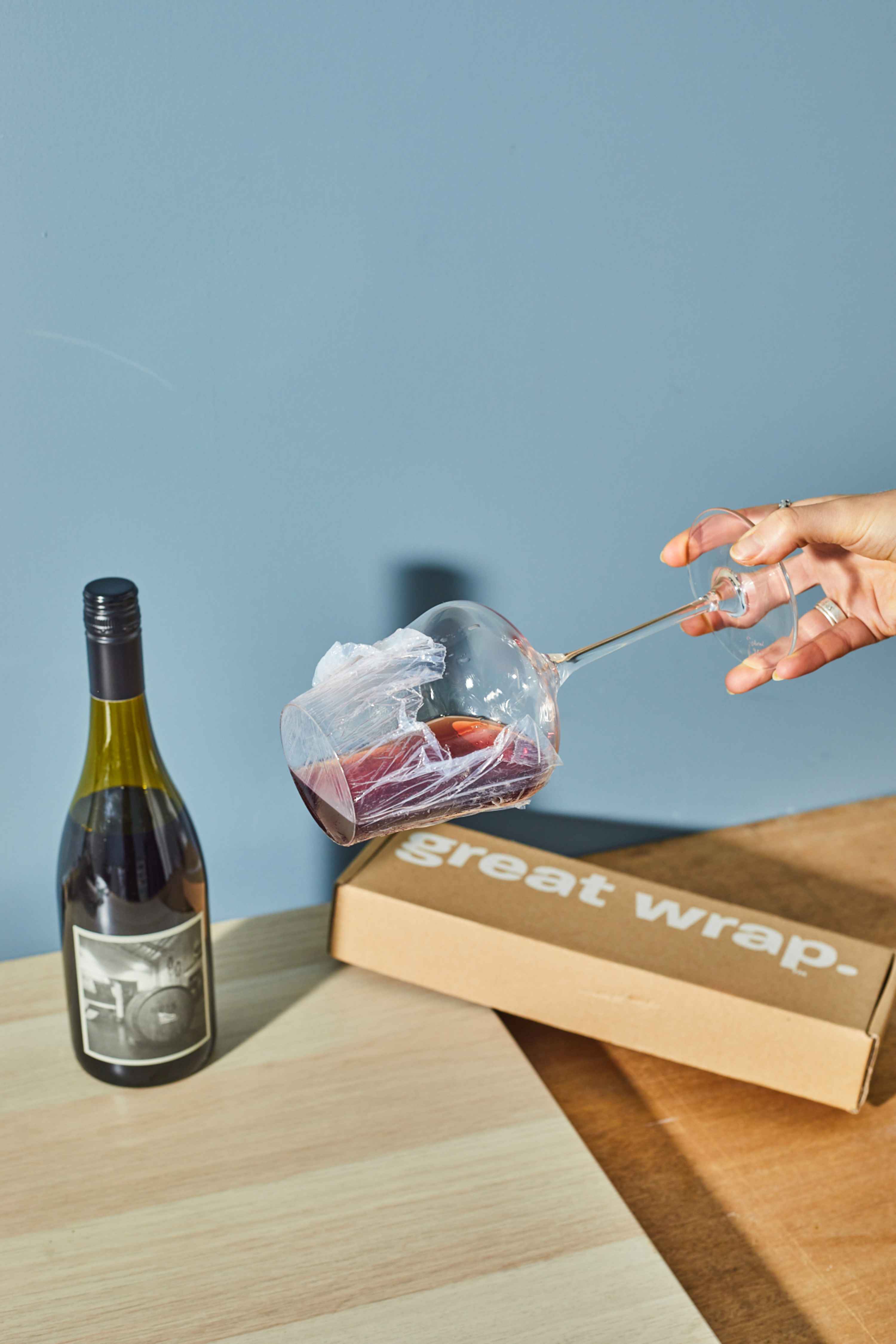
Hey Julia, can you start by telling us a little bit about how Great Wrap came to be and what inspired you both to move into creating your own products?
Well, Jordy was making natural wine and farming organically and I was working in architecture designing buildings with an education focus. We’d both used a lot of pallet wrap in our respective industries and in architecture I would spend a lot of time looking for the most sustainable materials only for them to arrive on site wrapped in pallet wrap made from petroleum based products, and it was the same for Jordy.
One day we were sitting on a beach and asked ourselves if we weren’t operating in our respective industries would they be any different without us. The answer felt like a no which was when we really decided to do something more meaningful for the planet and for ourselves. We both love spending time in the ocean so the plastic waste problem felt like a natural fit to tackle.
We wanted to test that there was an appetite for a product like ours and we knew we wanted to use it, but weren’t sure if this was actually a product the rest of the world cared about. So we had some pallet wrap contract manufactured and posted it on our own personal Instagram accounts - it sold out within hours! That’s when we knew we were doing something important.
It was after that moment that we decided we’d have to make it ourselves to ensure we could give customers the best products possible without making any sacrifices. Now we have a factory manufacturing it ourselves where we’re creating inclusive jobs and using renewables to power it.
Your factory sounds pretty special, can you tell us a little bit about what makes it unique?
You’re right it is pretty special! Our factory is 100% solar powered and it’s on the Mornington Peninsula! Jordy grew up on the Mornington Peninsula and we now live down there so it made sense to base our first factory there. We’re also the only factory in Australia that manufactures compostable cling wrap and we have the only machine that produces compostable wrap - we call her Nessy!

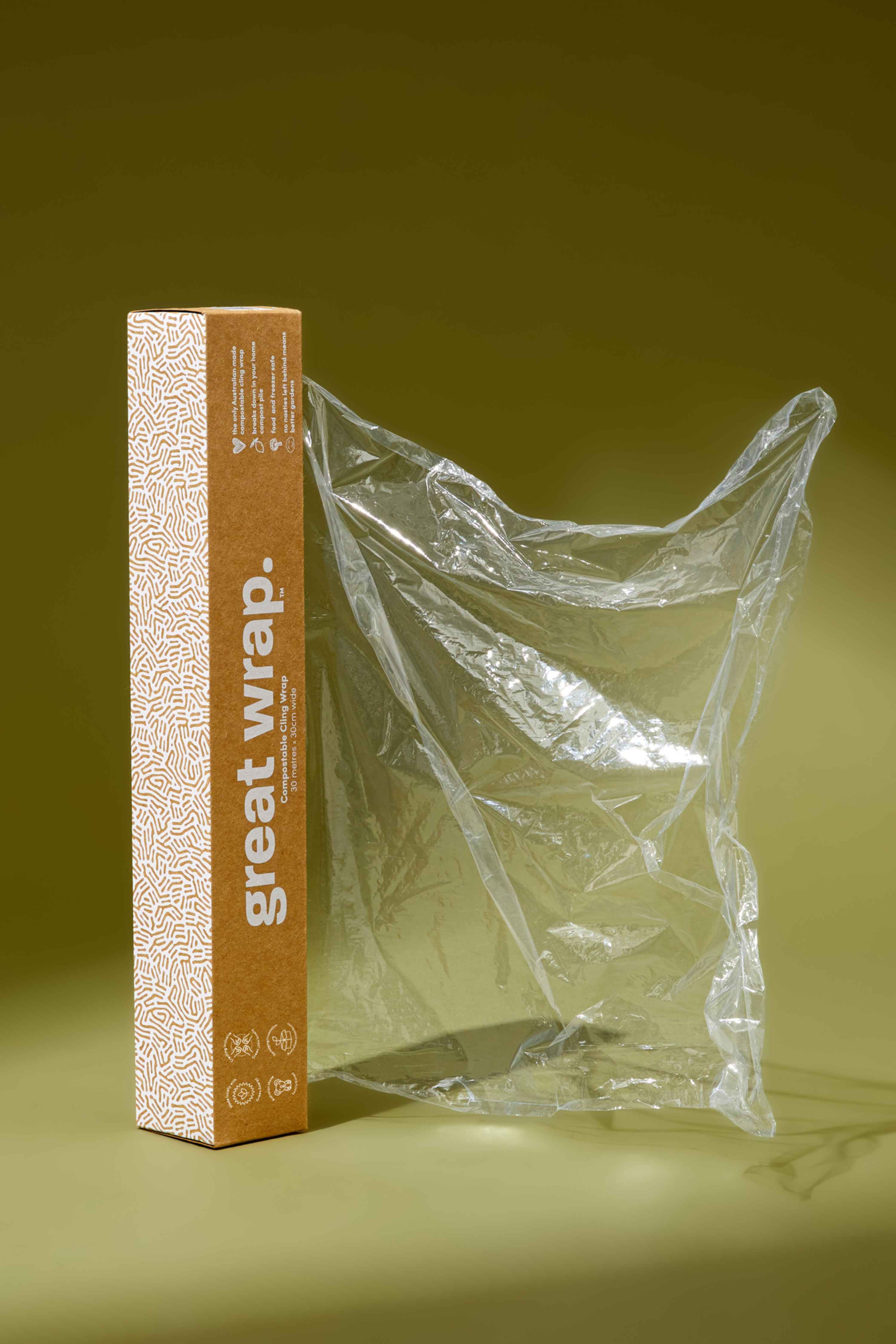
We hear a lot about biodegradable plastics and packaging, how does compostable wrap differ from this?
Biodegradable packaging is made from petroleum like regular plastic but has an organic additive that enables it to break down very easily when exposed to sunlight and moisture. The problem is that it breaks down to smaller pieces of plastic or microplastics! Compostable packaging, like Great Wrap, breaks down into carbon and water leaving no toxins behind. It’s made mostly from organic matter or in our case, food waste.
There are a couple of compost options, industrial and home. Industrial compostable packaging requires a compost environment with temperatures of about 60 degrees celsius to break down. If it does not reach these temperatures then it can take years to completely break down. Great Wrap is home compostable meaning it can break down in your compost pile at home in a matter of weeks. All it requires is a compost pile at ambient temperature to break down into carbon and water.
In terms of manufacturing, what key processes does Great Wrap go through to achieve the final product?
We use food waste to create our wrap, it’s mainly made of potato left over from french fries and chips! The potato waste that we use to create Great Wrap is processed into resin pallets offsite. This resin is then delivered to our factory on the Mornington Peninsula where our special formula goes through the extrusion process. This basically means our Great Wrap recipe is heated up and then stretched out into a thin film that gets rolled onto a cardboard roll like you would recognise (it kind of looks like honey before it’s stretched out). Once our rolls come off our machine our amazing factory team manages quality control and packs all of our orders. They’re the real heroes at Great Wrap!


Great Wrap has already been adopted by many domestic customers and you’ll soon have a commercial offering as well. How have you gone about building each part of your business?
We’ve seen so much growth over the past couple of years and we’ve been able to test and trial many different formulas and boxes to ensure we’re giving our customers the best product possible. We began manufacturing overseas last year but since the launch of our factory in April we have already converted over 10,000 homes to home compostable cling wrap and this is just the beginning for us!
We’re currently in the process of setting up our commercial side of the business and expect to launch our Pallet & Commercial wrap ready for Australians in Spring this year. We're so lucky to have had so much interest so far and there are so many unsuspecting industries like tattooists and hairdressers who have reached out for our compostable cling wrap.
It’s horrifying how many people use plastic cling wrap every day, but promising to see our waitlist grow as the days go by. We can't wait to start sending it out the factory door and see so many Australian businesses take a step closer to sustainability!


What’s next for Great Wrap and what are you looking forward to for the rest of 2021?
This year we’ll launch our Commercial & Pallet wrap, expand facilities across Australia and continue to work on our marine biodegradable solution with Monash University. By 2023 we aim to be making 1m tonnes of marine biodegradable and home compostable biopolymers, by then we’ll have started manufacturing other products, not just home and industrial wrap.